1. Introduction to Electric Servo Presses
An electric servo press is a modern industrial machine designed to apply controlled force with exceptional precision. Unlike traditional hydraulic or pneumatic systems, it uses a servo motor and advanced control technology to regulate speed, position, and pressure in real time. This makes it ideal for tasks requiring high accuracy, such as assembling delicate electronics or forming complex automotive components.
At its core, a servo-electric press operates through a combination of a servo motor, ball screw or belt drive, and programmable logic controllers (PLCs). The servo motor adjusts torque and rotation based on real-time feedback, enabling precise control over the pressing cycle. This eliminates the inconsistencies often seen in hydraulic systems, where fluid pressure variations can affect performance.
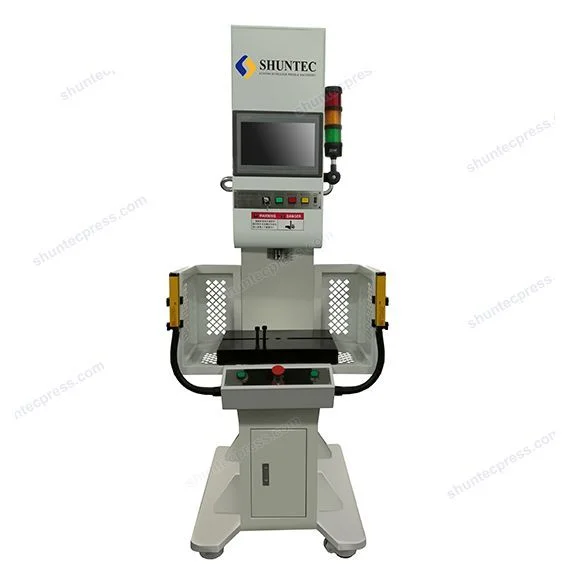
The shift from hydraulic to electric servo presses marks a significant evolution in manufacturing technology. Hydraulic presses, while powerful, consume more energy, require frequent maintenance, and lack the flexibility needed for modern precision tasks. Electric servo presses address these limitations by offering energy efficiency, quieter operation, and adaptability to diverse production requirements. Industries now prioritize these machines for their ability to reduce waste, improve product quality, and lower long-term operational costs.
As automation and smart manufacturing advance, electric servo presses are becoming central to industries aiming for sustainability and precision. Their role extends beyond basic pressing—they enable complex workflows, from micro-component assembly in electronics to high-tolerance applications in aerospace. This adaptability, paired with reduced environmental impact, positions servo-electric technology as a cornerstone of future-ready manufacturing.
2. Key Advantages of Electric Servo Presses
Electric servo presses have rapidly become a preferred choice in modern manufacturing, thanks to their ability to address longstanding challenges in precision, efficiency, and operational flexibility. Unlike traditional hydraulic or pneumatic systems, these machines leverage servo motor technology to deliver unparalleled control over force, speed, and positioning. This ensures consistent results even in high-stakes applications, such as assembling microelectronics or forming aerospace components, where deviations of mere micrometers can compromise product quality.
Energy efficiency is another standout benefit. Hydraulic presses often waste power due to continuous fluid circulation, while servo-electric presses consume energy only during active pressing cycles. This not only reduces electricity costs but also aligns with sustainability goals—a critical factor for industries aiming to minimize their carbon footprint. Additionally, the absence of hydraulic oil eliminates risks of leaks, lowering environmental hazards and cleanup costs.
Flexibility is a key advantage in today’s fast-paced production environments. Servo-electric presses allow operators to adjust parameters like stroke length and force on-the-fly via programmable interfaces. This adaptability makes them ideal for mixed-production lines, where a single machine can handle diverse tasks, from delicate medical device assembly to heavy-duty metal stamping. Manufacturers can also integrate these presses with IoT-enabled systems for real-time monitoring, further enhancing process optimization.
Maintenance demands are significantly reduced compared to hydraulic counterparts. With fewer mechanical components and no hydraulic fluid to replace, downtime is minimized. The simplicity of servo-electric systems also translates to longer service life and lower repair costs over time. Combined with their quieter operation and compact design, these advantages make servo-electric presses a cost-effective, future-ready investment for industries prioritizing productivity and innovation.
3. Common Applications Across Industries
Electric servo presses have revolutionized manufacturing processes across diverse sectors by combining precision, adaptability, and efficiency. In the automotive industry, these machines are indispensable for tasks like gear assembly, bearing installation, and sheet metal forming. Their ability to deliver consistent force ensures components meet strict safety and performance standards, while programmable settings allow automakers to switch between different production lines seamlessly.
The electronics sector relies on servo-electric presses for assembling delicate components such as circuit boards, sensors, and microchips. Even minor force variations can damage sensitive parts, making the precision of servo-driven systems critical. Manufacturers also use these presses for embedding connectors or sealing casings, where controlled pressure prevents overheating or deformation.
Aerospace applications demand extreme accuracy due to the high-tolerance requirements of aircraft and spacecraft parts. Servo-electric presses are used to form lightweight alloys, install rivets, and mold composite materials. Their repeatability ensures every component adheres to rigorous industry specifications, reducing the risk of defects in critical systems.
Beyond mass production, custom hydraulic and servo-electric press combinations cater to specialized needs. For example, medical device manufacturers use them to assemble surgical tools with micron-level precision, while renewable energy companies employ these systems for shaping turbine components. The flexibility to adjust force, speed, and stroke length makes servo-electric presses a versatile solution for niche or evolving industries.
As automation advances, these machines are increasingly integrated into smart factories, supporting everything from small-batch prototyping to high-volume production. Their role in enhancing quality and reducing waste underscores their growing importance in modern, sustainability-focused manufacturing.
4. Types of Electric Press Machines
Electric press machines are designed to meet varying industrial demands, with servo-electric models leading the charge in innovation. Standalone servo-electric presses are among the most popular, relying entirely on servo motors for precise control over force and motion. These machines excel in applications like electronics assembly or medical device manufacturing, where micron-level accuracy is non-negotiable. Their programmable interfaces allow operators to adjust parameters effortlessly, making them ideal for industries requiring rapid product changeovers or small-batch production.
Hybrid systems, such as custom hydraulic and servo-electric press combinations, offer a balance of power and precision. By integrating hydraulic force for high-tonnage tasks with servo-driven accuracy for delicate operations, these systems cater to industries like automotive or aerospace. For instance, they might handle heavy metal stamping while simultaneously ensuring precise alignment of components—a dual capability that traditional hydraulic presses struggle to achieve.
The distinction between compact and industrial-scale electric presses lies in their capacity and application scope. Compact models are space-efficient solutions for workshops or laboratories, often used for prototyping or low-volume tasks. In contrast, industrial-scale servo-electric presses are built for endurance, supporting high-volume production lines with consistent performance. Their robust design ensures reliability in demanding environments, such as automotive part fabrication or appliance manufacturing.
Emerging variations include IoT-enabled electric presses, which integrate with smart factory systems for real-time data monitoring and predictive maintenance. These advanced machines not only optimize production efficiency but also reduce downtime by alerting operators to potential issues before they escalate. Whether a business prioritizes precision, scalability, or adaptability, the evolving range of electric press machines ensures there’s a solution tailored to modern manufacturing challenges.
5. How to Choose the Right Electric Servo Press
Selecting the ideal electric servo press begins with understanding your production requirements. Tonnage, for instance, directly impacts the machine’s capability to handle specific tasks. A press with insufficient force may fail to form thick metals, while excessive tonnage could damage delicate components. Evaluate the maximum force needed for your applications, factoring in future scalability to avoid costly upgrades.
Speed and precision are equally critical. High-speed production lines, such as those in consumer electronics, demand servo-electric presses with rapid cycle times and real-time adjustments. Look for models offering programmable speed profiles to match varying workflows. For tasks like micro-component assembly, prioritize presses with closed-loop feedback systems to maintain accuracy under fluctuating loads.
Workspace constraints often dictate the press’s size and configuration. Compact servo-electric presses suit labs or small workshops, whereas industrial setups may require larger models with enhanced durability. Consider the press’s footprint, accessibility for maintenance, and compatibility with existing automation systems. Modular designs can offer flexibility, allowing you to add features like IoT connectivity as needs evolve.
Customizability is a game-changer for specialized operations. Suppliers offering tailored solutions—such as hybrid hydraulic-servo systems or custom tooling interfaces—enable adaptation to unique tasks, from aerospace part forming to medical device assembly. Assess the vendor’s engineering support and ability to integrate third-party software or sensors for advanced process control.
Finally, balance upfront costs with long-term ROI. While servo-electric presses may have higher initial prices than hydraulic alternatives, their energy efficiency, reduced maintenance, and productivity gains often justify the investment. Calculate potential savings from lower downtime, improved product quality, and compliance with sustainability standards. Partnering with a manufacturer that provides training and after-sales service ensures your press remains a strategic asset for years to come.
6. Maintenance and Safety Best Practices
Regular maintenance is essential to maximize the lifespan and efficiency of your electric servo press. Start with routine inspections of critical components like the servo motor, ball screw, and control systems. Look for signs of wear, such as unusual noises or vibrations, which could indicate misalignment or mechanical stress. Many modern presses include diagnostic software to monitor performance metrics, enabling proactive troubleshooting before minor issues escalate into costly downtime.
Lubrication plays a vital role in preserving moving parts. Follow the manufacturer’s guidelines for lubricant types and intervals, focusing on components like linear guides and bearings. Over-lubrication can attract debris, while under-lubrication accelerates wear. Similarly, replace consumable parts—seals, belts, or sensors—as recommended, even if they appear functional. Preventive replacements reduce the risk of unexpected failures during high-precision tasks.
Operator safety hinges on both equipment design and training. Ensure all personnel understand how to use emergency stop buttons and safety interlocks, which halt operations instantly if a hazard is detected. Regular drills on handling malfunctions, such as tool jams or power surges, build confidence and reduce panic responses. Personal protective equipment (PPE), including gloves and safety glasses, should be mandatory, especially during tasks involving high force or flying debris.
Lastly, maintain a clean workspace to prevent contaminants from affecting the press’s performance. Dust or metal shavings can interfere with sensors or clog lubrication points. Document every maintenance activity and safety incident to identify patterns and refine protocols. By prioritizing these practices, businesses not only safeguard their workforce but also ensure consistent productivity and compliance with industry regulations.
7. Future Trends in Electric Press Technology
The evolution of electric servo presses is being driven by advancements in automation, sustainability, and digital integration. One of the most transformative trends is the adoption of IoT (Internet of Things) connectivity, enabling real-time data collection and remote monitoring. Smart servo presses can now predict maintenance needs, optimize energy usage, and even self-adjust parameters based on production demands. This shift not only reduces downtime but also empowers manufacturers to transition toward predictive maintenance models, where issues are resolved before they disrupt workflows.
Sustainability remains a central focus, with manufacturers prioritizing energy-efficient designs and eco-friendly materials. Next-gen servo-electric presses are expected to incorporate regenerative energy systems that recycle power during idle phases, further slashing carbon footprints. Additionally, lightweight yet durable components, such as carbon-fiber-reinforced parts, are gaining traction to enhance efficiency without compromising durability.
Artificial intelligence (AI) and machine learning are set to revolutionize precision and quality control. AI algorithms can analyze production data to identify patterns, fine-tune pressing cycles, and detect microscopic defects in real time. This level of intelligence ensures consistent output in high-stakes industries like aerospace and medical devices, where perfection is non-negotiable.
Modularity is another emerging trend, allowing businesses to upgrade existing presses with new features rather than replacing entire systems. For instance, retrofitting older models with IoT sensors or advanced servo drives extends their lifespan while keeping pace with technological advancements. As industries embrace customization and scalability, electric servo presses will continue to serve as adaptable pillars of smart, sustainable manufacturing.
8. FAQs About Electric Servo Presses
What’s the difference between servo-electric and hydraulic presses?
Servo-electric presses use servo motors and digital controls to deliver precise force and speed adjustments, making them ideal for high-accuracy tasks like electronics assembly. Hydraulic presses rely on fluid pressure, which can lead to energy waste and less control. While hydraulic systems excel in high-tonnage applications, servo-electric models offer superior energy efficiency, quieter operation, and minimal maintenance.
Can electric servo presses handle high-tonnage tasks?
Yes, modern servo-electric presses are designed to handle a wide range of tonnage requirements. Advanced models can deliver forces comparable to mid-range hydraulic presses, particularly in industries like automotive metal forming. For extreme tonnage needs, hybrid systems combining hydraulic and servo-electric technologies provide a balanced solution.
Are servo-electric presses suitable for small businesses?
Absolutely. Compact servo-electric presses are cost-effective for small-scale production or prototyping, offering the same precision as industrial models. Their lower energy consumption and minimal maintenance reduce long-term costs, while programmable settings allow small businesses to adapt quickly to custom orders or changing demands.
How do servo-electric presses improve product quality?
By eliminating fluctuations in force and speed common in hydraulic systems, servo-electric presses ensure consistent results. Real-time feedback mechanisms adjust parameters during operation, preventing defects like micro-cracks in delicate components or misalignments in assembly processes.
What industries benefit most from servo-electric presses?
Industries requiring precision and flexibility, such as electronics, aerospace, and medical device manufacturing, gain the most. Automotive and renewable energy sectors also leverage these presses for tasks like battery assembly or turbine component forming, where repeatability and efficiency are critical.
Do servo-electric presses require specialized training?
While basic operation is intuitive, maximizing their potential often requires training on programmable interfaces and safety protocols. Many manufacturers provide onboarding support, and the integration of user-friendly software reduces the learning curve for new operators.
Are these presses compatible with automation systems?
Yes. Servo-electric presses are designed to integrate seamlessly with IoT platforms, robotics, and smart factory systems. Features like real-time data sharing and remote control align with Industry 4.0 trends, enabling fully automated production lines with minimal human intervention.
What is the typical lifespan of a servo-electric press?
With proper maintenance, these presses can operate efficiently for over a decade. Their durable construction and fewer moving parts compared to hydraulic systems contribute to a longer service life, provided routine inspections and lubrication schedules are followed.
9. Conclusion
Electric servo presses represent a transformative leap in manufacturing technology, merging precision, efficiency, and adaptability to meet the demands of modern industries. Their ability to deliver consistent force and speed adjustments ensures high-quality output across applications—from delicate electronics assembly to robust automotive part forming. As industries increasingly prioritize sustainability and automation, these machines stand out for their energy efficiency, reduced maintenance, and seamless integration with smart factory systems.
For businesses considering adoption, the key lies in aligning press specifications with operational needs. Whether investing in compact models for prototyping or industrial-scale systems for mass production, the focus should be on scalability, customizability, and long-term ROI. Equally important are proactive maintenance and safety protocols, which safeguard both equipment and personnel while maximizing uptime.
As technology evolves, trends like IoT connectivity, AI-driven optimization, and modular upgrades will further enhance the capabilities of servo-electric presses. By embracing these innovations, manufacturers can stay ahead in a competitive landscape, driving productivity while reducing environmental impact. Ultimately, the shift toward electric servo presses isn’t just a technological upgrade—it’s a strategic investment in a smarter, more sustainable future for manufacturing.