Introduction
Hydraulic systems have a fundamental role in many industries, ranging from construction and manufacturing to aviation and shipping. The heart of these systems lies in the ability to transmit power through the use of pressurized fluid. This role demands the fluid to be clean, and it is here that hydraulic filters come into play. Their function is to maintain fluid cleanliness by removing contaminants, ensuring efficient operation and longevity of the system.
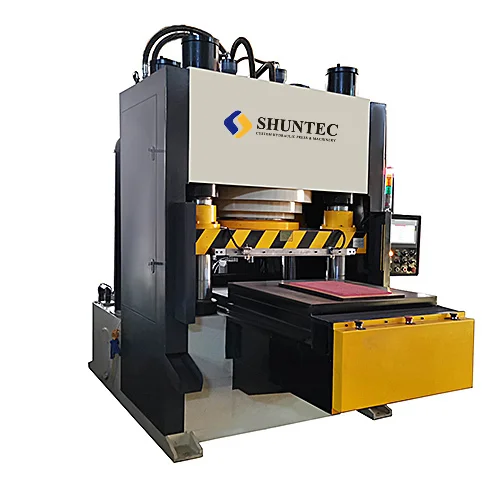
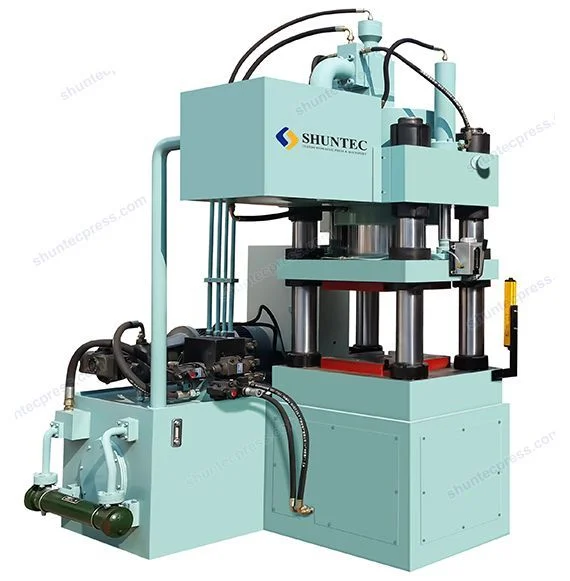

Number of Filters in a Hydraulic System
The number of filters in a hydraulic system can vary significantly based on the complexity of the system. Typically, there are at least two primary filters in a basic hydraulic system – the suction filter and the return filter.
The suction filter, positioned in the suction line, is the first defense against contaminants entering the pump from the reservoir. The return filter, located in the return line, captures any debris generated in the hydraulic system before the fluid returns to the reservoir.
In more complex systems, there may also be pressure filters, offline filters, and breather filters. Each serves a unique function, all aiming to minimize system contamination and optimize performance.
Diversity in Hydraulic Filters
Not all hydraulic filters are the same. They vary based on factors such as filtration mechanism, filtration rating, construction, and placement within the system.
Filtration Mechanism
The way a filter removes particles can be surface filtration, where particles are captured on the surface of the filter media, or depth filtration, where particles are captured within the filter media’s thickness.
Filtration Rating
This refers to the smallest particle size a filter can effectively capture. It’s typically measured in microns.
Construction
Some filters are designed to be disposable after use, while others have a reusable filter element that can be cleaned and reinstalled.
Placement
As mentioned earlier, filters can be located in different parts of the hydraulic system (suction line, return line, pressure line, etc.).
Each filter type has its pros and cons, and the choice depends on various factors such as the hydraulic system’s nature, the type of fluid used, and the level of cleanliness required.

Overview of Hydraulic Systems
There are primarily two types of hydraulic systems – open-loop and closed-loop.
- Open-Loop Systems: In these systems, the fluid flows from the reservoir to the hydraulic pump, gets pressurized, and is then directed to the actuator (cylinder or hydraulic motor) through the control valves. After performing work, the fluid is returned to the reservoir, and the cycle continues. Open-loop systems are common in industrial applications like hydraulic presses, conveyor belts, etc.
- Closed-Loop Systems: These systems are more complex. The hydraulic fluid flows from the pump directly to the actuator and back to the pump in a continuous loop, without returning to the reservoir after every cycle. This design is often seen in mobile applications like excavators and aircraft controls, where high efficiency and compactness are essential.
Classification of Filters
Filters can be generally classified into four categories based on their function:
- Strainers/Screens: These are coarse filters that primarily remove larger particles and are often used as preliminary filters before the fluid reaches finer filters.
- Surface Filters: These capture contaminants on the filter media’s surface. They’re commonly used when high filtration efficiency is required.
- Depth Filters: These capture contaminants within the depth of the filter media. They have a high dirt-holding capacity and are often used in applications where the contamination level is high.
- Adsorption Filters: These remove dissolved contaminants from the fluid via a chemical reaction. These filters are used in applications where the fluid’s purity level is paramount.

Hydraulic System Filters
Within hydraulic systems, there are several specific types of filters:
- Suction Filters: Located in the suction line, these filters protect the pump from contaminants in the reservoir.
- Return Filters: Placed in the return line, these filters capture contaminants before the fluid is returned to the reservoir.
- Pressure Filters: These filters protect sensitive components downstream of the pump by removing fine contaminants.
- Offline (Kidney Loop) Filters: These filters continuously filter fluid from the reservoir, independent of the main hydraulic system, providing an additional level of filtration.
- Breather Filters: These filters protect the hydraulic fluid from airborne contamination.
Conclusion
The role of hydraulic filters is indispensable in maintaining the efficiency, performance, and lifespan of hydraulic systems. They come in various types, each serving a specific purpose, and understanding their function and proper placement is crucial in optimizing hydraulic system performance.
Regardless of the type of hydraulic system in use – whether open-loop or closed, the appropriate selection, maintenance, and regular replacement of hydraulic filters can help prevent downtime, reduce maintenance costs, and extend the life of the system components.